
CNC machine can operate in either absolute (X, Y, Z) or incremental coordinates (U, V, W). For instance, Figure 1.2 is a 5-axis setup. In general, A, B, and C are rotational axes that rotate around axes formed by the X, Y, and Z respectively. Note that in Figure 1.2 bellow, we have added two rotational axes to the basic mill diagram to provide an A-Axis and a B-Axis. Much more complex configurations are possible when we have more axes.

Note: arrows show table motion in positive g-code direction. ‘A’, ‘B’ and ‘C’ are the rotary axis of motion ‘XY’, ‘XZ’ and ‘YZ’ are planes of operationįigure 1.1: Mill Axes for a Typical Vertical Machining Center. 1.1 Coordinate systemĮach machine come up with its own specific axis orientation which we should become familiar with. (2007) argued that, machine tools such as lathe, grinder, router and mill are programmable using such a language. A machine unit is a small computer used for storing and for executing the G-code (Shin et al., 2007). The table with the vice holding the work-piece follows the coordination system while the cutting tool remains stationary - the cutting tool can only move in the vertical direction.
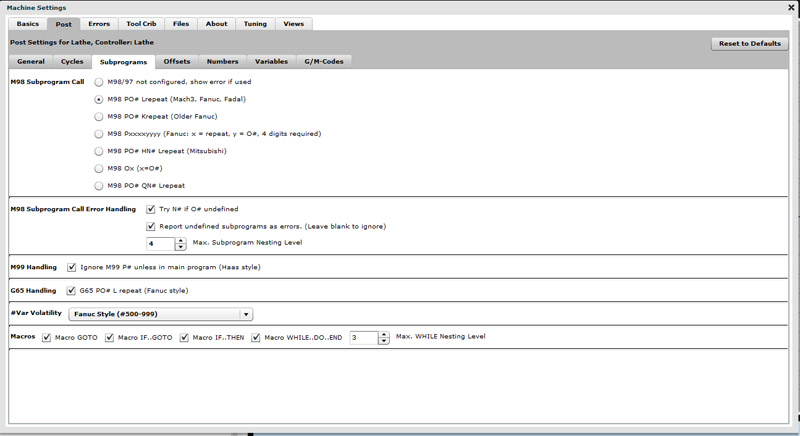
The part program contains a set of instructions (G-code) written using a CNC machining language to control various features of the machine tool such as location, coordination, speed and input parameters such as the feed rate, depth of cut and so forth (Shin et al., 2007). Machine tool The hardware that receives instructions from the Machine Control. The Part program Set of instructions produced to produce a part. A computer numerical control system is made up three components: 1 This process is mostly used in manufacturing industries. Chapter 1 IntroductionĪccording to Jacobs and Haberman (2017), Computer Numerical Control (CNC) machining is a process that involves the use of computers to control machine tools.
CODIGOS CNC SIMULATOR CODE
We learnt from the demonstration that the shorter the constructed code the more robust it is, using a bigger tool is more efficient in terms of saving energy and time, and that if the code is correct the CNC machine model becomes identical to that of the product Design. The cutting time was affected by the complexity of the design, chosen tool size and the cutting technique. The main problem that was experienced was the cutting time the model took longer to be complete. We used foam for our model and a 10 diameter end mill tool. The logo was further modified with the final model drawn using Auto Desk Inventor. Prior to the machining process, we did a Computer Aided Design (CAD) draw- ing of the Mercedes Benz logo. The task was to choose and design a creative item to be machined using CNC machining, which then required to write a code using CNC language.

This report covers the work that was carried out by a group of researchers 1 on CNC (Computer Numerical Control) programming and machining. ġ.5 Machining pattern (Author’s own work)ġ.6 Engineering drawing of the Mercedes Benz logo (Author’s own work)Ī.1 Machine utilized (Author’s own work) List of Tables ġ.4 3-D model of the Mercedes Benz logo (Author’s own work). (Author’s own work)ġ.2 5-Axis Mill With Trunion Table (Author’s own work)ġ.3 Mercedes Benz logo (MEYERS and O’DONOHUE, 1973). Note: ar- rows show table motion in positive g-code direction. 1.2 Advantages and disadvantages of CNC machiningĪppendices Appendix A CNC machine and G-Code used 13ġ.1 Mill Axes for a Typical Vertical Machining Center.
